Understanding a Certificate of Analysis: An In-Depth Guide to Quality Assurance
Written by: Hunter Podell, Subject Matter Expert and Website Founder
Published: March 15, 2024; Last updated: April 6, 2024
- 1. Key Takeaways
- 2. The Role of Certificates of Analysis in Quality Assurance
- 2.1 Regulatory Agency Requirements
- 2.2 Customer Confidence and Trust
- 3. Types of Industries Utilizing Certificates of Analysis
- 3.1 Agricultural Industry
- 3.2 Chemical Industry
- 3.3 Food Industry
- 4. Critical Components of a Certificate of Analysis
- 4.1 Test Results and Specifications
- 4.2 Material Supplier Information
- 4.3 Specific Characteristics
- 5. The Process of Obtaining a Certificate of Analysis
- 5.1 Choosing an Accredited Laboratory
- 5.2 Submitting Samples for Testing
- 5.3 Receiving and Reviewing the COA
- 6. Potential Issues Caused by Not Using a Certificate of Analysis
- 6.1 Product Recalls and Legal Issues
- 6.2 Loss of Customer Trust
- 7. Best Practices for Managing Certificates of Analysis
- 7.1 Storage and Organization
- 7.2 Updating and Maintaining Records
- 8. Summary
- 9. Frequently Asked Questions
- 9.1 What is the difference between COC and COA?
- 9.2 Is a COA a legal document?
- 9.3 What is a CBD Certificate of Analysis?
- 9.4 Does The CBD Joint list products that have COAs?
- 9.5 Why are Certificates of Analysis essential?
- 9.6 In which industries are COAs commonly used?
- 10. References
Navigating the complexities of quality assurance across industries hinges on the critical role of a Certificate of Analysis (COA). A COA is not just a piece of paper; you guarantee that a product meets stringent specifications for safety and quality — a non-negotiable in today’s regulatory landscape. This foundational guide unpacks the significance of COAs, revealing how they cement consumer trust, comply with regulatory demands, and serve across various sectors, from CBD oil to pharmaceutics. Dive into the essential elements of a COA and the steps required to secure this pivotal document, all while discovering its undeniable impact on the market.
Key Takeaways
- Certificates of Analysis (COAs) are critical documents for ensuring product quality and regulatory compliance across industries, including agriculture, chemicals, food, and pharmaceuticals, effectively fostering consumer trust and confidence.
- COAs contain vital information such as detailed test results, material supplier details, and specific product characteristics, which are integral for traceability, accountability, and verifying that products meet safety and efficacy standards.
- Proper management and regular updating of COAs are paramount for maintaining regulatory compliance and product quality, with COA management software offering solutions for efficient storage, organization, and record-keeping.
The Role of Certificates of Analysis in Quality Assurance
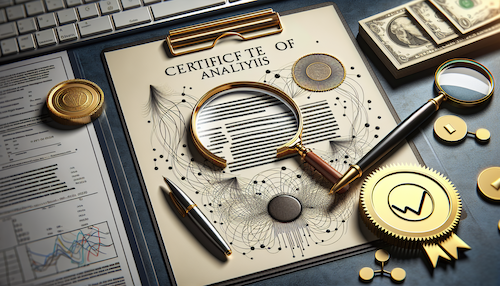
Certificates of Analysis play a paramount role in quality assurance. A COA is at the heart, whether it’s a food product aiming to meet safety and quality standards or a chemical product needing to showcase compliance. It is concrete evidence of conformance, outlining specific characteristics, test results, and compliance statements.
It’s a testament to the product’s compliance with established specifications based on the evidence presented.
Regulatory Agency Requirements
COAs are exceptionally vital for demonstrating compliance with regulatory requirements. For instance, the food industry ensures products meet the stringent regulatory compliance needed for import and export transactions. Regulatory agencies such as the FDA mandate that COAs for food products contain essential information like:
- the manufacturer’s name
- product name
- batch number
- detailed test results aligned with specified acceptance limits.
Customer Confidence and Trust
COAs do not just meet regulatory requirements; they also instill consumer confidence. Confirming that products adhere to specifications and regulatory requirements gives customers peace of mind regarding product identity, quality, and purity. Without a COA, customer confidence can wane, leading to skepticism about the product’s safety, performance, and sustainability.
Therefore, accurate COAs contribute to maintaining customer confidence, offering protection against competitive disadvantages and potential product recalls, and helping to assure customers of product quality.
Types of Industries Utilizing Certificates of Analysis
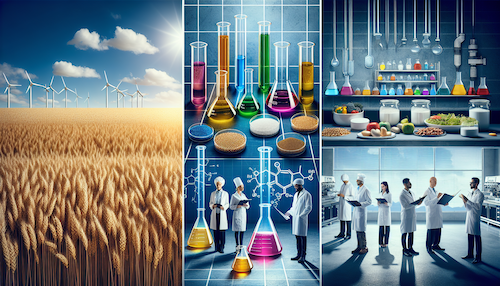
The utilization of Certificates of Analysis, including CBD certificates, spans various industries, from agriculture and chemical products to clinical research, food and beverage, and even the pharmaceutical sector.
For example, in the booming CBD industry, COAs have become an industry standard crucial for establishing product safety and quality, especially for CBD oils and other CBD products derived from the hemp plant.
Agricultural Industry
In the agricultural industry, COAs serve an integral role in ensuring that seeds, fertilizers, and pesticides meet quality standards and abide by legal limits for safety. By verifying that these products comply with safety standards and regulations, COAs bolster confidence and trust amongst farmers and consumers alike.
Chemical Industry
In the chemical industry, COAs serve as a competitive edge. Companies that produce Certificates of Analysis can retain more customers by demonstrating a commitment to safety and quality. Hence, COAs become a tangible testament to a company’s dedication to maintaining high safety and efficacy standards.
Food Industry
COAs in the food industry serve as product identification documents, providing more details than labels. They are used in transactions to verify that products meet prescribed standards, ensuring that the food on our tables is safe and of high quality.
Critical Components of a Certificate of Analysis
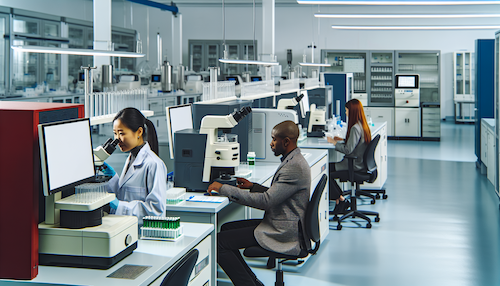
A Certificate of Analysis is more than a single page of information. It’s a comprehensive document that includes critical components such as test results, material supplier information, and specific product characteristics. Each of these components makes products more accessible to trace and helps provide visibility on the source and quality of materials used in the product.
Test Results and Specifications
At the heart of a COA are the test results and specifications. These detail the analytical results, showcasing whether products meet established quality and safety specifications. For instance, COAs in the chemical industry confirm the purity of chemicals and indicate the presence of contaminants like heavy metals or pesticides to ensure safety and efficacy.
This section includes information such as the type of tests conducted, the results stated in measurement units, and whether the tested products have passed or failed the specified criteria.
Material Supplier Information
Supplier information is a crucial part of a Certificate of Analysis. It establishes the traceability of the material and ensures accountability. This section should contain the supplier’s name, address, and other contact information. Including agreed-upon standards within this section is essential for demonstrating that the materials meet predetermined quality benchmarks.
Specific Characteristics
The specific characteristics section of a Certificate of Analysis is crucial for the identification and traceability of the product. This section includes essential details such as lot numbers, product codes, and product descriptions, which aid tracking and traceability. A COA also provides specific data on the product’s physical, chemical, or biological characteristics to define its quality.
Expected performance standards are also documented for reference purposes.
The Process of Obtaining a Certificate of Analysis

Obtaining a Certificate of Analysis is a multi-step process that includes the following steps:
- It selects an accredited laboratory that adheres to industry standards such as ISO 17025:2017.
- The laboratory undergoes a rigorous assessment and is granted a certificate of accreditation, a testament to its ability to perform tests reliably and to international standards.
- The accredited laboratory performs the necessary tests and analysis to generate a valid Certificate of Analysis (COA).
This process ensures that the COA is accurate and reliable, providing valuable information about the quality and composition of the tested product.
Choosing an Accredited Laboratory
Choosing an accredited laboratory is not just about picking any lab that offers testing services. Accreditation is an independent assessment of a laboratory’s competence, distinguishing it from certifications or approvals, which may not include an on-site evaluation. The accreditation process for ISO 17025:2017 involves:
- Application
- Document submission
- Initial assessments
- Corrective actions
- Final approval with a quality management system documenting essential policies and procedures.
To ensure independent verification of product quality, manufacturers should choose laboratories accredited for the specific tests required for their products.
Submitting Samples for Testing
Once an accredited laboratory is chosen, samples must be submitted for testing. Understanding the required sample quantity for testing is crucial to meet testing parameters. The sample quantity needed varies based on product type and the specific tests to be conducted. Laboratories typically provide submission guidelines that include the required samples for analysis.
The laboratory may provide special containers or preservation methods to ensure the sample remains in good condition during transportation, adhering to specific shipping requirements.
Receiving and Reviewing the COA
The final step in obtaining a COA involves receiving and reviewing the document. A Certificate of Analysis must provide the following information:
- The company name selling the product
- The most recent test date
- A lot number that corresponds with the tested sample and its associated lading number
- Repacking or reprocessing details
- The original manufacturer’s information
Please ensure all this information is shown on the COA before accepting it.
Documenting receipt, calculating purity, utilizing reference material, and confirming information through a second-party QC review is essential.
Potential Issues Caused by Not Using a Certificate of Analysis

Skipping the use of a Certificate of Analysis can lead to severe repercussions. Failing to provide a COA can lead to fines, product recalls, or even legal action in industries with strict regulations. Additionally, a lack of COAs can make the audit process more complicated and less efficient.
When products are recalled or placed on hold due to lack of a COA, auditing and resolving the issue can take longer, potentially increasing costs.
Product Recalls and Legal Issues
The absence of a Certificate of Analysis can result in product recalls, which waste company time and resources and cause financial and reputational losses. Legal issues may arise if products comply with quality and safety standards, especially without a COA to validate their specifications.
While the FDA and the European Medicines Agency do not mandate formal regulatory qualifications for COAs, their use is encouraged to support labeling claims and maintain compliance with regulations.
Loss of Customer Trust
A critical impact of not providing a COA is the potential loss of customer trust. The absence of a Certificate of Analysis can seriously undermine customer and consumer trust, damaging the perception of a brand’s commitment to quality and safety.
Not providing a COA can result in lost customers and a weakened standing in the industry, which could incur higher costs than the investment in producing COAs.
Best Practices for Managing Certificates of Analysis
Proper management of Certificates of Analysis is as essential as obtaining them. Failing to store and organize COA properly can lead to confusion and errors, hindering quality control processes. They should be categorized by product name, batch number, and expiration date to facilitate efficient management and retrieval.
Moreover, updating Certificates of Analysis with the most current information is critical to maintaining regulatory compliance and product quality.
Storage and Organization
COA management software often includes the following features:
- Report designer for creating and tracking various document layouts tailored to customer needs
- Customization of COAs using user-defined fields to track specific customer requirements
- Data templates for selecting and grouping quality data to ensure accurate presentation of the COA
These software solutions provide a comprehensive solution for managing and customizing COAs.
Such management systems maintain an archive of all generated COAs, source data, certification identification numbers, and PDF copies, which can be accessed through search and inquiry tools.
Updating and Maintaining Records
Regularly reviewing and validating COAs to ensure they comply with the most current regulatory standards is essential to maintain their relevance in quality assurance. When updates or changes in COA content occur, it is critical to document these inconsistencies as they may impact historical study data, ensuring a robust internal process for such updates.
COA management software can quickly generate accurate reports, demonstrating that products meet or exceed customer specifications, which is essential for maintaining updated and compliant records.
Summary
We’ve journeyed through the world of Certificates of Analysis, uncovering their importance in quality assurance, their role across various industries, particularly in the cbd and hemp industries, their key components, the process of obtaining one, the impact of not using a COA, and best practices for managing these essential documents. It’s clear that COAs are more than just pieces of paper; they’re a testament to a product’s quality, safety, and compliance with regulatory standards. As we navigate an increasingly complex global market, the significance of COAs will continue to rise. So, the next time you consider a product — food, cosmetic, or agricultural seeds — ask for its Certificate of Analysis. It’s your right to know what you’re consuming or using.
Frequently Asked Questions
What is the difference between COC and COA?
The main difference between COC and COA lies in their purpose: COC ensures compliance with regulations and safety norms, while COA provides detailed test results and analysis to highlight product quality and safety.
Is a COA a legal document?
Yes, a COA is a legal document that provides proof that a product meets client’snt’s required criteria and expectations, serving as a formal laboratory-prepared document.
What is a CBD Certificate of Analysis?
A CBD Certificate of Analysis is a report from an accredited laboratory that details the chemical analysis of a CBD product, ensuring its safety and quality. It is generated for each batch of CBD products.
Does The CBD Joint list products that have COAs?
The CBD Joint takes great care to manage and maintain the integrity of products on our website. As such, all of the products we promote follow regulatory guidelines and have a COA.
Why are Certificates of Analysis essential?
Certificates of Analysis (COAs) are necessary because they assure customers, manufacturers, and suppliers that a product meets agreed-upon standards, enhancing customer confidence and trust.
In which industries are COAs commonly used?
COAs are commonly used in agriculture (CBD), chemical, clinical research, food and beverage, and pharmaceutical sectors.
References
Wikimedia Foundation. (2024, February 9). Certificate of analysis. Wikipedia. https://en.wikipedia.org/wiki/Certificate_of_analysis

Written by Hunter Podell - Subject Matter Expert and Website Founder
Hunter has 8+ years of experience as a content writer and digital marketer. Earning his chops marketing in the healthcare space for over 5 years, Hunter is extremely familiar with the rules and regulations required to deliver high quality content that answers the user's needs while adhering to strict guidelines.
Join the CBDeals Club!
Get 10% off your first order and receive our best and exclusive promotions directly to your inbox!